另据调查,在我国,轿车包括一些微型车,除汽车车身底漆都采用阴极电泳涂料,基本完全实现水性化外,中涂漆和面漆基本上全是溶剂型涂料。而在欧美国家,所有底漆、80%以上的汽车中涂漆、50%以上的闪光底色漆已经实现水性化。根据2012年北京家具协会的一项数据调查,家具行业的水性木器漆占比仅仅为8.3%。但中国涂料协会和水性木器漆产业联盟的目标是希望明年能达到15%。在涂装应用方面,水性涂料的市场也谈不上乐观。毕竟自1996年德国都芳漆率先将水性涂料引进中国后,水性涂料在中国已经耕耘有18载,但在市场占比和应用程度上,交出这样一份单薄无力的成绩单,确实说不过去。
问题出在哪里?知名评论人黄少东曾指出,任何一个产品的发展要形成一个市场,前提是必须要有支撑这个产品发展的产业链条的存在。否则,任何单一环节单一企业的努力,都不足以推动这个产品的快速发展。也就是说,水性涂料的发展必须要有支撑水性木器漆发展的产业链条存在。全球涂料网认为从现实来看,水性涂料的发展目前依然主要靠政策鼓励和生产企业推动,下游应用企业和终端消费渠道长期没有建立起水性漆的完善利益网,更多时候是迫于环保需求的无奈选择。这种被动选择注定成就不了水性漆市场的繁荣。
除市场认知度有限外,性价比以及企业转型成本也是导致水性涂料市场反应冷淡的主要因素。溶剂型涂料因为入行门槛相对较低,小规模油漆厂商数量众多,且经过长久以来的市场竞争磨合,使油性漆价格处于市场竞争的优势。而从油性漆变水性涂料,生产线改造的资金、时间、人工等高额成本,并非所有品牌都能轻易承担。展辰涂料技术总经理刘建平表示,溶剂型油漆改为水性涂料后,一件家具成品的生产成本大致上升5%,再加上改造生产线上千万的成本,企业的压力不小。一位不愿意透露姓名的家具工厂负责人则表示,如果必须要进行水性涂料技改,对中小型家具品牌而言,不提高家具售价将很难生存。
然而,伴随国家加强环境治理,企业节能减排的压力也随着加大。涂料的研制与生产必将走向环保化、多功能化和高性能化,而水性涂料也将成为今后涂料市场发展的主流。在“家具水性化”介绍酒会上,昆山白玉兰家具董事长沈忠民做了油性涂料和水性涂料的VOC比对。溶剂型实色漆工艺,按照7道工艺程序计算,涂布量为1300克/平方米,VOC为853.3克/平方米;水性实色漆工艺,按照6道工艺程序计算,涂布量为530克/平方米,VOC仅43.36克/平方米,比溶剂型的涂布率降低了59.23%,而VOC则降低了94.92%。同时,产品合格率也提高到99%。各种安全隐患,如火灾、粉尘、职业健康等风险也全部大大降低。尽管前期投入成本较大,但从改造后的综合成本来看,对企业的长远发展是很有利的。
在水性涂料浪潮下,面对反应平淡的市场,涂料企业应当拿出更多的热情,积极顺应低碳环保的大趋势,未雨绸缪、做好准备。消费者和涂装工用惯了油性漆,虽然水性涂料的环保性能获得普遍认可,但水性漆的物理性能和涂装效果却令人担心。这需要涂料企业通过终端渠道加强市场引导和舆论宣传,用事实、效果来说服和转变消费者观念,联合组织开展涂装工水性涂料技术培训,使水性涂料的涂装应用更加方便和理想。另外,水性漆因为是新产品,产量相对较少,原材料基本从国外进口,价格昂贵,导致涂料企业的生产压力和和市场的消费压力很大。涂料企业要通过自主创新、技术研发等多管齐下降低水性涂料的成本。
“现在涂料厂家和涂料应用企业的衔接很紧密,但是和设备厂家的衔接就比较疏松。像铁路警察一样,各管一段,没有有机结合起来”深圳市家具协会副理事长江展威认为,上下游企业要联合技术攻关,共同推动家具、汽车等各个制造业领域的水性漆普及。水性涂料跟油性涂料的施工工艺不同,需要水性涂料生产厂家、使用厂家与设备生产厂家共同努力,根据水性涂料的特性,设计生产出合适的工艺、合适的设备,降低生产线改造成本。只有通力合作,打造好水性涂料的市场利益链,水性涂料市场才能根本扭转冷清的局面。
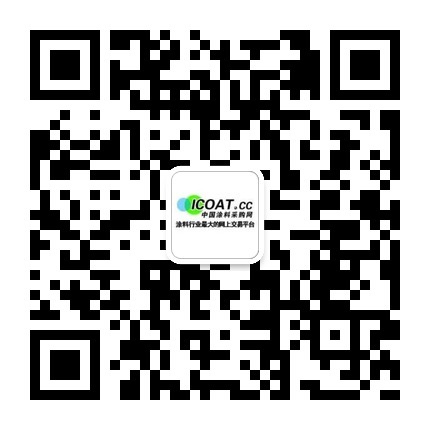
欢迎关注“中国涂料采购网”官方微信订阅号:icoat2014,中国涂料采购网是涂料行业访问量最大的门户网站。关注中国涂料采购网,掌握涂料行业实时动态!