2014年中国经济软着陆,GDP增长为7.4%,是中国24年来最低的一个增长率。中国汽车工业也由2013年的产增长率14.76%和销增长率13.87%回归到7%-8%这一普遍预期的增速水平。中国2014年生产汽车2372.29万辆,同比增长7.3%,销售汽车2349.19万辆,同比增长6.9%,产销量保持世界第一。
联想到2011年和2012年中国汽车销售增长率分别为2.5%和3.2%,2013年的13.87%增长似乎有点不可思议,其实这一增长主要出现在2013年下半年特别是9月份开始迅速上升,持续到年底。当时是在一个特殊的“北上广津”等多个大城市限购限行之时,由此催生的刚性需求推动了短暂的车市爆发性增长。从过去四年的产销趋势可以初步推断出中国汽车工业可能已开始步入一个新的成长模式--中速成长的新常态。
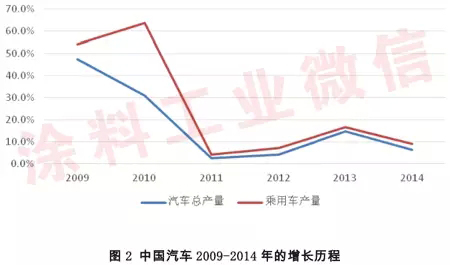
我国汽车产销突破1000万辆,用了半个世纪。而从2009年的1000多万辆到2014年的2300万辆,仅用了4年时间。从2000年的200万辆到2300万辆,仅用了14年时间。2014年我国汽车产销创历史新高,比2013年汽车产量净增160.61万辆和销量净增150.78万辆,产量和增速均再次刷新全球记录,并已连续六年蝉联全球第一。
数据显示,2014年乘用车产销分别达到1991.98万辆和1969.7万辆。乘用车销售稳定增长,同比增长8.9%。其中:基本型乘用车(轿车)产销1248.11万辆和1237.67万辆,同比增长3.14%和3.06%;多功能乘用车(MPV)产销197.27万辆和191.43万辆,同比增长49.35%和46.79%;运动型多用途乘用车(SUV)产销416.65万辆和407.79万辆,同比增长37.70%和36.44%;交叉型乘用车产销129.95万辆和133.17万辆,同比下降20.61%和18.06%。产业的集中度进一步提升。中国乘用车总的趋势延续稳定增长,其中,主要由于轿车增速放缓,SUV、MPV依旧保持高速增长,交叉型乘用车则继续下降。
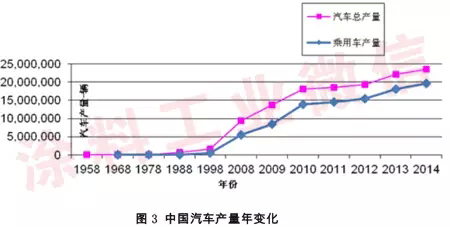
2014年,受到合资企业生产的外国品牌汽车在新车推出数量的增加和推出速度上的加快、中小型车推出力度的加大以及产品价格下探等因素的影响,中国品牌车市场份额持续下降,产业的集中度进一步提升。合资公司的市场份额继续增长,特别是德美车系和韩国车系。我国自主品牌乘用车销售757.33万辆,同比增长4.1%,占乘用车销售市场的38.4%,市场份额同比下降2.1个百分点。其中自主品牌轿车销售277.44万辆,同比下降17.4%,占轿车市场的22.4%,市场份额同比下降5.6个百分点。自主品牌车系仅长安汽车一枝独秀,其他自主品牌的市场份额有明显下降的趋势,长城汽车和吉利汽车等都跌出前十名。但中国品牌SUV市场份额上升,成为年度亮点。
2014年商用车与2013年相比,客车产销增长较快,货车小幅下降。客车产销60.72万辆和60.69万辆,同比增长7.63%和8.37%。其中:大型客车产销8.35万辆和8.42万辆,同比增长2.02%和3.15%;中型客车产销7.88万辆和7.96万辆,同比下降14.28%和11.62%;轻型客车产销44.49万辆和44.31万辆,同比增长13.96%和14.10%。
货车产销319.59万辆和318.44万辆,同比下降7.86%和8.92%。其中:重型货车产销74.75万辆和74.40万辆,同比下降1.73%和3.89%;中型货车产销24.79万辆和24.78万辆,同比下降13.16%和13.60%;轻型货车产销166.16万辆和166.27万辆,同比下降12.31%和12.87%;微型货车产销53.89万辆和52.99万辆,同比增长2.17%和0.55%。
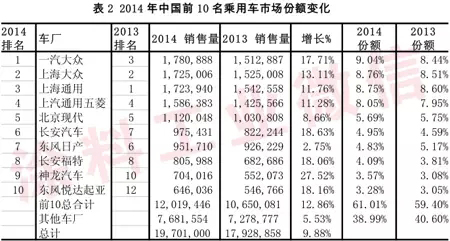
汽车涂装的技术进步
环境友好型材料的普及应用:应用硅烷/锆盐前处理材料,无铅、高泳透力、高平滑性阴极电泳漆,高性能自泳漆,粉末涂料,水性/高固体份中涂,水性/高固体份底色,高固体份清漆,水性修补漆等一系材料,可在满足越来越高的质量要求的前提下,彻底结束涂装排放大量重金属和有机挥发物的历史。随着节能高效新技术的应用,加快了汽车涂装绿色环保的发展进程。
紧凑工艺已经作为新的标准工艺应用:紧凑车身涂装工艺是与传统工艺比较而言,各涂料公司及汽车公司都有自己的商标名称,实质大同小异。主要在传统工艺的基础上,通过涂料性能的优化和相应涂层膜厚的调整,取消中涂烘干(即所谓的3Wet、3C1B、PPCG2工艺等)或完全取消中涂线(即免中涂、Ecoconcept、B1B2、IPⅡ、2010工艺等)。免中涂工艺并非简单地取消中涂,它是在不降低综合涂层性能前提下,实现了资源消耗的减量化,使用聚氨酯清漆和在基色漆中添加吸能材料,可以吸收石击的能量,在清漆中添加紫外线吸收剂,在基色漆中增加颜料浓度及采用两层底色,可阻止紫外线透过面漆层,改进包括电泳漆在内的所有涂料的填充性和漆膜平滑性能,满足装饰性要求,通过对基色漆和罩光清漆改良,将中涂的基本功能集成到底色和清漆涂层。
材料工艺的创新:非金属材料(如塑料,复合材料等)件在车身上应用比例越来越大,由于低温固化(80℃,20min)工艺有助于实现非金属件与车身共线涂装,同时又可降低烘干能耗,所以,应用高性能低温固化双组份聚氨酯涂料将成为一种趋势。具有无光(亚光/MattColour)、抗划伤(自复原/SelfHealing)、自清洁(不沾灰尘)、变化闪耀感(Flip-flopeffect)、深厚立体感(DeepFeeling)等特性的面漆将成为一种时尚,促进涂料及工艺的不断创新。覆膜技术越来越广泛地用于多色装饰和塑料覆盖件,部分取代传统面漆喷涂。BMW公司最新上市的i3电动车车身已经完全由覆膜技术取代了传统的面漆喷涂。
汽车涂料工业的发展情况
2014年是中国汽车涂料工业稳中增长的一年,除了乘用车的增长外,商用车中轻型客车的较大幅度的增长带来了车身原厂漆的需求增长,而货车整体市场的下行则抵消了这部分的增长量。由于国内产能的增加和国产化的进展不足,2014年原厂汽车漆的进口部分在下降,主要是原材料和半成品的进口为主,以及新引进的产品体系如水性紧凑型涂装技术产品。
2014年中国汽车涂料原厂漆的用量约在50-55万吨(不包含农用车,摩托车和三轮车等低速货车用涂料)。在细分市场的用漆比例中轿车仍然是原厂汽车漆最大的用户,占总量的50%,见图4。其次是多功能运动车20%,货车涂料占17%和巴士用涂料占5.2%。在统计各原厂汽车漆的品种的变化中我们发现,中涂层漆的使用量没有同比例上升,电泳漆的比例也在下降,见图5。这主要是由于欧美系车厂采用了紧凑型工艺省略了中涂层或降低了中涂层膜厚,新的涂装线使用的杯加杯的自动涂装机器人节省15%的涂料使用量。高泳透力电泳的使用也使电泳漆的单车耗量有所降低,但是客车涂装开始从传统溶剂型防腐底漆转型为性能更好的电泳漆。
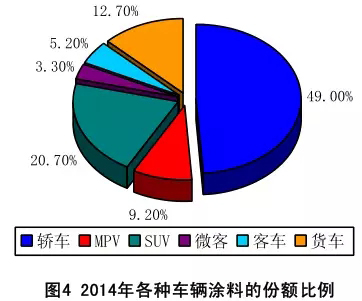
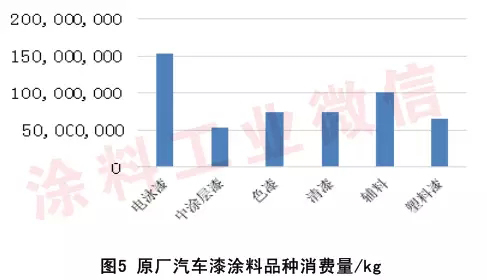
汽车涂料工业的升级和发展
由于中国汽车工业进一步向上汽,东风和长安汽车等大汽车集团集中,与之配套的汽车涂料生产的集中度正在加快,艾仕得涂料,BASF,PPG,关西,立邦和KCC这六家国际和地区涂料制造商原厂漆市场中的格局没有大的变化。2014年中国主要的汽车涂料原厂漆制造商见表3。涂料制造商的动态:2014年11月,艾仕得涂料系统(AxaltaCoating System)在美国纽约证券交易所上市,这是在全球另类资产管理机构凯雷集团(纳斯达克股票代码:CG),以49亿美元完成其对杜邦高性能涂料业务部门的收购后,在仅仅18个月后就实现了新公司的上市,是近20年来在纽交所上市的最大的化工公司。
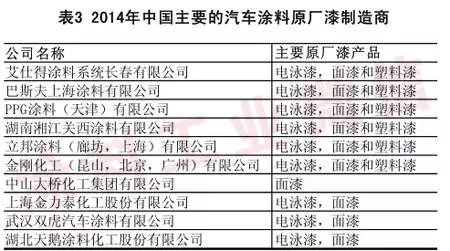
中国2014年前十名的乘用车公司尽管在前几年都投资建设了新工厂,新增加的产能不能满足市场的需求,新的汽车工厂的投资仍在继续以弥补产能上的缺口。而所有这些新涂装线,都是按照国家的新标准要求设计的,大部分都采用了最新的精益涂装技术和工艺,以保证达到35g/m2的VOC排放限制。
中国新汽车工厂的投资和投产带动了汽车涂料新技术品种的需求,主要国际汽车涂料制造商都在中国加大了投资力度。BASF上海涂料公司在2014宣布投资上海金山化工区新工厂开业不久,就又宣布追加投资增加产能,并在上海BASF高桥工厂内增加电泳漆树脂和面漆树脂的生产能力。
2014年1月10日,艾仕得涂料系统宣布在上海将投资逾5,000万美元建设新水性OEM原厂涂料生产装置正式破土动工,预计将可为快速拓展华中和华南市场的汽车制造商生产和供应多达25000t涂料。新工厂将专注于打造Axalta(艾仕得)涂料系统的水性涂料产品,此类产品同时满足汽车制造商及监管部门所制订的环保标准。并将于2015年第一季度正式投产。
2014年10月22日,PPG工业公司与河南佰利联化学股份有限公司在河南焦作举办了盛大的落成典礼,庆祝河南佰利联钛白粉生产研发基地正式竣工。这座新工厂定于2015年第一季度正式投产,将使用氯化法工艺大批量生产钛白粉产品。工厂总面积达36.6万m2,钛白粉年产量预计将达10万t并可根据需要进行扩产。PPG计划在油漆和涂料产品的生产中使用该工厂的钛白粉。此外,新工厂中还设立了一个12000m2的技术研发中心,主要用于钛白粉在涂料领域的应用研究。研发中心的设立也将加强两家公司的紧密合作,在新工厂内加快新一代氯化法钛白粉的研发、测试及认证。2012年,PPG与河南佰利联签署了一项合作协议,PPG将向后者提供氯化法技术,帮助其成立氯化法钛白粉生产基地。此外,PPG还与河南佰利联签订了长期供货协议,承诺将向该公司采购钛白粉产品
就在2013年底湘江关西涂料建设的水性漆车间和研发大厦竣工交付使用得同时,湘江关西涂料计划投资新的制造基地已经开始建设,预计投资超过10亿元人民币,总产能将达到约20万t。新工厂预计在2016年部分投产运行。
国际和地区涂料制造商进一步在中国扩大先进汽车涂料的生产产能,建立技术中心和研发中心,在中国进行产品的研发本地化的实际举措,说明汽车原厂漆开始进入深度国产化的阶段。中国汽车涂料工业正在从单纯的中国制造开始走向中国研发制造阶段。